Ep. 632 - Ammunition for Hunters, Designed by Hunters – Behind the Scenes with Winchester
Mike Brasher: Welcome back, everyone. I am your host on this episode, Dr. Mike Brasher, and I'm on location in East Alton, Illinois. Fanatics of ammunition may recognize that as being the home of Winchester. This is the headquarters for Winchester, right? Yeah, that's correct. And so, just got back from a phenomenal sort of behind-the-scenes tour of the Shot Shell Manufacturing Facility here, and we're gonna talk with three people that are, it's really impressive. I'm looking around, they've got their red shirts on, their gray shirt, and they're all, they have the classic Winchester logo. I was making the comment earlier that Winchester has the most iconic logo in the ammunition business, in my opinion there, so I'm sure y'all will agree. I'm gonna start with introductions here and just kind of go right around the table. And so Nathan, I'll let you go first. Just introduce yourself. Sure. What do you do for Winchester?
Nathan Robinson: I'm Nathan Robinson. I'm one of the marketing managers and I work with events and retail and media relations. And one of the highlights is working with Ducks Unlimited, managing that partnership and our relationship with you guys.
Ben Frank: And go right here, Ben. Ben Frank, I've been from Winchester for 22 years. I started in engineering, so actually in shot shell engineering. So, I'm excited to talk about some of the stuff we've done in the past on waterfowl. Now, I'm in charge of really all of the products for Winchester. That's rifle, pistol, rimfire, and shotgun shells. So, we've got facilities here in East Alton, but we also have a facility in Oxford, Mississippi, and then we also run the Lake City Army Ammunition Plant. And then to my right.
Grant Jeremiah: Hi, I'm Grant Jeremiah. I am the supervisor of Shot Shell New Product Engineering. I'm excited to talk about some of our advancements in waterfowl. As a big waterfowl hunter myself, this is something that definitely excites me and pretty proud of what we've got out there today.
Mike Brasher: So, Winchester Ammunition, the official ammunition of Ducks Unlimited. If you're out buying Winchester Ammunition, which we encourage you to do, you will find some boxes out there that have the Ducks Unlimited logo on it. We saw some of those in the plant earlier, and it's always really cool. I'm wearing my DU logo shirt, and you're walking through an ammunition factory, and you see a box, the most iconic logo from the ammunition. from the ammunition business and there's the Ducks Unlimited logo. It's a really cool pairing and so we appreciate your partnership.
Nathan Robinson: Not something easy to get access to. If you know anything about Winchester's history, we've supported DU I think from the very beginning. It's hard to know for sure because those are some old records, but our predecessors were involved with some of the very first conservation groups and the starting of the conservation movement in the United States. and helped start some of those predecessors to DU. And we've been there for decades supporting at a large level. And that DU logo on the packaging is just kind of a testament to that. And we thank DU for letting us use it. And we're thankful that some of the proceeds from our sales get to help support conservation and the future of waterfowl hunting.
Mike Brasher: Yeah, that's what it's about here in terms of this partnership. We're all waterfowl hunters. We all understand the importance of waterfowl hunters in supporting conservation. through a lot of different means. And you just talked about one of those through this partnership that does provide resources back to the conservation that we put on the ground. And we want to talk a little about that as we get into this conversation. There's a number of things that we could discuss. Like I said, a fantastic tour of that facility. My head was spinning as we were listening to, what was the guy's name that we were talking with that was leading us through the tour? Matt Richardson. Matt Richardson. He's like head engineer or something of that nature?
Grant Jeremiah: He actually runs all of our manufacturing in Chowchill there.
Mike Brasher: Okay, is he an engineer, kind of by training? Yes, he did have an engineering background. He certainly spoke as though he was an engineer, the way he was rattling off. And I'm glad he didn't hold me to the test that he was saying was going to come at the end of that. East Alton, Illinois. Nathan, you were telling me that you've been here, you've been part of Winchester for 14 years. That's right. You are the resident historian.
Nathan Robinson: I was really born into Winchester, though, because my grandpa was a diehard Winchester guy, and he was a competitive shooter. And so, from my earliest memories out on the range, it was with Winchester Products, and that's one of the things that attracted me to the company, is I had that loyalty already kind of bred into me from the beginning.
Mike Brasher: I want to talk about the relationship, the longstanding… It's in the blood, I guess you could say, waterfowl hunting and wanting to advance the products that waterfowl hunters rely on and how that's in the blood of Winchester. and it dates back to the founder. So, I want you to talk about that, all the different connections that he had to waterfowl hunting. And so, who wants to take that first?
Nathan Robinson: You want to take that? I think we can kind of tag team it. I mean, it really goes back, that innovation and engineering mindset that is part of our DNA goes back to Oliver Winchester. And so, in 1866, he founded the company, and that was on the cusp of a lot of new technology in the gun space, specifically. And then, as the company grew, they began doing ammunition. And a few decades later, a small company in East Alton, Illinois, led by Franklin Olin, started out as blasting powder, and then he added ammunition to it that became the Western ammunition brand. They took over ownership of Winchester, I think in 1931 or thereabouts, and at that time, you start to see the thumbprint of John Olin on the business. So at that time, that's one of Franklin Olin's sons. He was a diehard hunter and shooter and loved our industry and everything about it, but he was also an engineer. And so he started out with the company developing products alongside his employees. And then that culture just really took off from there. ducks was a big part of it. He loved his place down in Stuttgart, and every free moment he got, he was down there hunting with some iconic labs, and it's kind of the history of Winchester, and a thing that we still are reminded of today, because it's part of how we were brought into the limelight, and everybody that's been successful has that same DNA and that same drive for innovation and a passion for hunting and shooting.
Mike Brasher: And I think there's a connection to retrievers as well associated with this.
Ben Frank: Who wants to talk about that? His passion towards hunting kind of led into this passion towards retrievers and then he really, the Nilo farms, we have 640 acres here that was basically a field. There wasn't anything really there at the time. And he wanted to create a place where he could train the best retrievers in the world to really kind of fuel that waterfowl passion of his. But then it became a passion to really have the best of the best dogs. And you can do some research on Olin and Nilo and King Buck and things like that. And there's some really cool stories. If you go to Nilo, we still have all the trophies out there. But again, it just kind of was rooted in that passion for waterfowl hunting.
Mike Brasher: And if you haven't figured it out, Olin is… Nilo spelled backwards or vice versa, right? I guess Olin came first and Nilo came after.
Ben Frank: It looks a lot different today than when he bought it. I mean, it's all lots of trees. We grow it up now. We, we, you know, put Milo out there and we cut lanes and we still train dogs out there. We don't do any of the retrieving trials anymore, but there's some of the best dogs that you'll ever meet when you go out there to a time out at Nilo. And it's, it's a great time. We still have a duck shoot that's out there. They're basically at the facility and you go out there and we have different blinds set up, but the water fouling is still there. There's upland birds there. And then we also have trap and skeet and sporting clays. And it's just, it's a great place for the avid hunter and shooter to go from a history standpoint, Winchester and
Mike Brasher: waterfowl hunting, what are some of the other more notable things that we may not know about? Is there anything that comes to mind?
Nathan Robinson: Well, tied with Nilo, I can say that I mentioned his connection with conservation. He had a conservation department that spent a lot of time at Nilo taking that grazing ground, overgrazed, dead dirt and grass, and turning it into a wildlife oasis. And through their testing, they developed a lot of pamphlets that were early introductions to how you can improve your properties or start your own game preserve or how you help overwintering birds. They tested different types of grains and different types of habitat. and really were one of the first resources to start that conservation discussion. And that's tied, too, to Sammy. If anybody knows, that's Sporting Arms and Ammunition Manufacturers Institute. John Olin was the president of that and used the resources of the whole industry to start that conservation movement because it was a personal passion of his.
Mike Brasher: The other connection to conservation, and the thing that connects multiple items here we've talked about, the retriever side of things, conservation, the duck stamp. I think there's a dog that's featured on one of the stamps, right? I think I know where you're going. Yeah.
Nathan Robinson: So, King Buck is arguably the most famous lab of all time. And he was on the duck stamp, I think in 1959. He was a multi-time national champion lab, still the most winningest lab of AKC history. And so he's got a special place in the history books for us. Absolutely. And what you're referring to, I think there, if I can take over your train of thought is that we were recognized, or more importantly, the role of the duck dog was recognized by putting them on the duck stamp as a conservation tool. And it's such an important piece to not lose those ducks that you've fought so hard to trick into your decoys and taken a shot at, and you don't want them wandering off. So the dog is an invaluable tool to the waterfowl owner.
Mike Brasher: It's just another really impressive connection between John Olin and Winchester and and conservation for ducts. The duct stamp, of course, as we've talked about many times on the podcast, is probably the single most efficient mechanism for conserving waterfowl habitat on the prairies. I buy multiple duck stamps a year, and you're right, that iconic stamp of 1959 is the only time a dog has been featured on the duck stamp. It's the only time a dead duck has been featured on the duck stamp as well. It has a connection back to here, which is pretty cool. And so, I want to shift gears a little bit here. sort of extend this, I guess, to Winchester's leadership in waterfowl ammunitions. We were kind of sitting here a few moments ago and talking about the things that we wanted to discuss on this. You all were rattling off all the different components that go into a shot shell and how Winchester has sort of Because you're waterfowl hunters and you understand the rigors that waterfowl hunters put ammunition through and put guns through, you know the quality that needs to come along to produce a reliable ammunition, a reliable shot shell. So we're talking about everything from powder to plastics to wads. So who wants to kind of launch us down this history of how Winchester really established itself as the leader in innovation and thought and development for better waterfowl shot shells.
Ben Frank: I can start. I mean, if you think about it, Winchester has really been a pioneer in the waterfowl ammunition industry since the beginning. I mean, you go back to before steel shot. So, when people were hunting waterfowl, a lot of times they're using four and five lead. Then, come early 90s, all of a sudden, that's not a thing anymore. They figured out that, hey, lead's probably not the best thing to have in the wetlands, so now we have to use non-toxic shots, say. Well, really, that's steel. And up until that point, people who were using steel were just having all kinds of problems with it. It didn't really perform very well. You couldn't get high enough energy and velocity out of it. And so even just working on the powders back then and working on the componentry that goes into those different shells was Winchester's at the forefront of that. Because again, it's such a near and dear, you know, use of, you know, game for the per people here at Winchester that it's like, we got to figure out a way to make this game better. And we need to build a better mousetrap. And we have all of these things at our fingertips to be able to do that. And that goes to the powder. I mean, arguably throughout the industry, you're not going to find anyone who's had that much impact on each of the different components that almost everyone is able to use today came from a lot of the technology testing that we did from an engineering side of things way back when, and we still continue to do that today.
Grant Jeremiah: I'd like to jump right in there. I mean, like Ben said, one of the big things going from lead to steel, I mean, when you, when you think, Oh, I can't be that hard. You just, pull the lead out and throw the steel in. Well, there's a huge difference there. I mean, when you look at the density of lead, you're looking around 11 grams per cubic centimeter, you go to steel, you're 7.8. So the volume difference there is quite vast, quite large. So that requires new wads. And then whenever you get into removing that hinge section to allow that extra volume change in that wad, now you got to change your powders and go to a slower powders that might not ignite as easy compared to traditional lead powders. That volume difference there just really changed the game. And that's where we had to start coming and looking up these new designs for different wads, different powders, looking from, you know, single base to double base powders. And then, which then gets you to the next thing of, well, steel shot definitely is a lot harder than lead. And that definitely had some issues with barrels back in the day, going from lead shot that, you know, people didn't, weren't protecting their bores. Well, now that's something we had to start looking at. So, right away, we developed some shot cups to help support that steel and not allow it to penetrate through and damage barrels. And that's something we still continue to this day. All of our steel shot cups are made out of a high-density polyethylene that's thicker and it's more designed for steel and harder shot. protect barrels and it's something that general people aren't going to think about, but in the background, it's things that we've done to make sure that your shells aren't going to damage your gun and it's going to give you a good hunting experience.
Mike Brasher: So, what does that process look like where an idea, you're trying to come up with an idea to improve performance of some aspect of a shot shell? Do you get a group of engineers sitting around the table and drawing on whiteboards or chalkboards back in the day and just sort of skunk works type laboratory type thing?
Grant Jeremiah: Yeah, there's definitely that. There's definitely also, you know, we have consumers that come to us with questions and we try to find answers for. But yeah, generally we try to get together as a group and, you know, this isn't an individual effort. I mean, everybody's got their own individual experiences that we all bring to the table. And we sit around and try and figure out, you know, the best path forward. And then, you know, we as engineers, we've always got that engineering mindset going on. We definitely try to question everything and get data and do some testing and get some results and figure out what's going to be the best. the best way forward. And you can continue to see that today with some of our newer products. I mean, our bismuth that just came out, I mean, that's by far up there as one of the top bismuths on the market. And then you got our new Last Call TSS we just announced this year, best duck load available.
Mike Brasher: I have shot the Bismuth. I can attest to its quality. Love the shot shell. Love what it does. I think I've shot it in three different gauges now. 28, 20, yeah, and 12. And they're all wonderful. TSS, the last call I've not shot yet, that is brand new on the market this year, right?
Grant Jeremiah: Correct. We just announced that September 5th of this year.
Mike Brasher: How long does it take to go from the idea of a last call, of a TSS load, to getting it to market?
Grant Jeremiah: It depends on the individual product. Some of it can be really quick, especially if it's a simple change, but something new, there's a lot that goes into it. Not only from an engineering standpoint, but from a marketing standpoint and manufacturing standpoint as well. So, some of those can take a little while, but generally we try to keep everything as short and as concise as possible. But with this last call, I mean, we've had that in the back of our mind for a while now. Uh, and we finally decided the market was right. And we got engaged with, you know, manufacturing as well as marketing and engineering. We got everybody together and decided, Hey, what's the best game plan to go forward with this? So right at the beginning of water fallacies, and that's when we decided, Hey, this is perfect time. We're going to announce this, have ammo basically ready on the shelves. So people can see the new announcement and go out, pick some up and try it right in the field right away.
Mike Brasher: Anybody that's on social media will probably have seen one or more posts from a number from Ducks Unlimited or any of our other partners sort of advertising with a little promo for last call. I saw the filming of that back at our headquarters when we were doing that. It's exciting to see that come to market for Winchester.
Nathan Robinson: No, it definitely is exciting. But what I think is a cooler testament to Winchester is that this happens every four to six years. Like we're constantly innovating. And so I've been here 14 years and I've seen multiple new product innovations. And if you look at that across pistol and rifle, really every year there's some game-changing innovation that we're bringing to market. And sometimes it feels like a lot for us to manage, but we want to make sure that we're bringing the most high-tech solutions to our customers possible so that we're leading the industry in that way. And that's just been something that has always been part of the company and a driving force for us going into the future.
Ben Frank: Yeah, and I'll say Grant kind of alluded to it, but we do a lot of iterative design. And what that means is we do a lot of just testing that you can draw down on paper, but there's no exact equation that's going to tell you the right answer. The only way you're going to figure it out is you got to try it and you got to go shoot it. and you go shoot patterns and you shoot it through different choke tubes and you shoot it through aftermarket choke tubes. You shoot it at different ranges. We shoot gel. And the cool thing about having Nilo is we get to go shoot actual birds and we can pretty much tell what range they're at. And it's a really kind of isolated situation, but it's great for us to be able to tell how that stuff is working. And we've been doing that stuff really since Nilo's been around and it's a great tool for us, but that's really kind of how we do it. I look back on, like you said, products that we've come out with over time. I was lucky enough to work on Blindside back when I was an engineer in Shot Shell. And one of the things was just taking shot cups cutting slits in them and figuring out how does this heck shot work and what kind of wad situation is going to help this through all different kinds of choke tubes. And that's how we came up with the diamond cut wad at the time, which was pretty cool because it's just us sitting there, cutting things down, taking it right back to the lab, shooting paper and finding out you know, what's it doing? And we tried multiple different designs to try to make that work. But again, it was a lot of fun. And then the hex shot itself, we were talking about it before we started talking here, but me and another engineer, Steve Meyer, you know, he's been, was around for a lot of these developments, but we're sitting there throwing flywheels by hand, one at a time, making individual pellets of hex shot. different dimensions and trying to figure out exactly what's going to work the best. Basically, flipping this flywheel to make enough to make six or seven shells worth one at a time and go shoot patterns. And that's the kind of stuff that we've done over time and then working with our suppliers to figure out a way to make that in mass quantities so that that way we can bring blindside and products like that to the market at a price that's affordable that we can really kind of get out there across all of our customers and get them the best waterfowl products possible.
Mike Brasher: that's exactly what you thought you were going to be doing in your career whenever you were back in college, studying for engineering, right?
Ben Frank: You know, I actually interned at Olin in the brass mill, and I knew a lot, and I'm from this area, kind of like Nathan, and so knowing that Winchester's here and growing up with a lot of different people in the community who've had fathers and mothers that have worked at Winchester, even my aunt, whenever I first started in Shotshell, my aunt actually worked in the Shotshell area there, which is kind of neat because I show up and from a little kid, I knew she worked there and now all of a sudden I'm working here as well and working on some really cool stuff and then getting to take it out in the field. I mean, we were talking about it before, but our engineers, our marketeers, going back even before we all started, those folks get out there and they hunt together. They were very critical of our own products. So we go out there and we want to be shooting the best of the best. And we want to be out there in the field succeeding just as much as you guys do. And that means a lot to us across the board. I mean, even when I was in grant can probably attest to this, to this day, we've got people out on the floor who run our equipment, who are also waterfowl hunters, and they are very much in tune with how this stuff performs. They want to know how it's patterning. They want to know how this new wad is working. So, how last call is, even though it can be a little pricey, they want to hear that if I'm going to spend that money, it's got to be the best of the best and they're out there making sure that happens.
Mike Brasher: Yeah, we're in a pretty good location here for like historical waterfowl hunting, right? Right on the Mississippi River, Southern Illinois. There's probably been a few ducks killed around here.
Ben Frank: Yeah, I would say that probably, you know, 15, 20 years ago was a little bit better than it is today.
Mike Brasher: Let's not go there.
Nathan Robinson: Southern Illinois used to be the main goose hunting place in the country. Yeah, it's still good, but I'd like to see it be a little bit better.
Ben Frank: Illinois probably needs to do a little bit more to help bring those waterfowl back here because it's kind of shifted over to the Missouri side. Our Missouri friends are probably like, thank you for letting the birds come here. We're good.
Mike Brasher: Check the next issue of the Ducks Unlimited magazine. It should be hitting the mailboxes this week. There's actually an article in there called Ducks on the Move. It'll be out by the time this airs. And then there's companion webpage associated with that. Talks about this very thing. We used some six decades of Bay and Recovery data to look at whether the distribution of harvest of different species has changed, and it has, just a spoiler alert in some ways, but it depends on a few other things. So anyway, it's interesting that we kind of landed it. That's kind of the area that I can talk a lot about. I think that right there sort of typifies who you are. You're in tune with it. You work, you're an engineer at Winchester wanting to develop these fantastic products because you use them. And you use them, you're a diehard waterfowl hunter, you're not gonna ask me that question and know that issue if you're not a diehard waterfowl hunter and haven't been doing it for a long time. And I know it extends beyond you and all of you. Many others in the company. I guess I wanted to talk a little about that aspect of it. It takes a team to do what you do. We saw a lot of different people just in that one shot shell facility. There are multiple facilities here in East Dalton. How many, can you tell me about how many people you employ here? How important is Winchester to this area? How much pride do you think the people around this area have?
Grant Jeremiah: Yeah, just here in East Alton, it's north of 800 people just here. But as Ben said earlier, we also have our center fire operation down in Oxford, Mississippi, and we also run the Lake City Army Ammunition Plant currently. I believe we are actually the smallest of all the Winchester facilities.
Ben Frank: Really? Yeah. Any given time, there's between 3,500 and 4,000 employees for Winchester across those three different locations. And here in East Dalton, we make all of the shot shells, but we also make all the primers and our distribution center is here. And that's another really key component that a lot of people kind of forget about is primers. Because again, when you're talking waterfowl hunting, we don't use the same primer that we use in target loads just because to get those powders to do what we want them to do consistently at temperatures, we do things to them to make sure that they're going to be consistent. Also, water resistance is another piece of that puzzle. But yeah, I mean, we have… a wide range of people here in this location. We even make all of our lead shot here and over. We have one of the only, maybe two, three shot towers here in the United States, but it's pretty cool to watch shot get dropped like rain and metered out. sent over to the facility. You saw some of it today in big barrels, and then we sent them down to the loader right here. So, it takes a lot of people to be able to do all those things, and not just people on our end. We have great suppliers that help us get components, you know, whether you're talking powder, whether you're talking like raw lead, whether it's working with our plastic suppliers. I mean, it takes a lot of people to be able to make the shot shells and as many shot shells as Winchester makes.
Nathan Robinson: Well, and you mentioned the iterative design when you've got almost 160 years of experience doing something, you keep building on that knowledge. And so you see this continuing evolution because we're just building on the people that came before us and newer companies don't have that knowledge base and expertise to draw from.
Mike Brasher: So as we were doing the tour, the one thing that really stood out to me was the number, and this gets to kind of what you were talking about, all of these decisions, all of these innovations that are made through time. I was asking questions. I mean, it was a phenomenal tour. information was coming at me at 1,000 miles an hour. Decomposing shot shells of different types to every single component, the thickness of the plastic, the source of the plastic, the way the wad is cut, the makeup of the primer, learned about how the primer actually functions, those types of things. shells when I was younger, 20 gauge, 12 gauge, so I was able to kind of keep up with some of what we were talking about. But the number of decisions that go into every aspect of that, and it's not just… How many products? Can you tell me how many products y'all have? Because however many products you have, how many decisions go into it, there's your multiplier there. It's an incredible number, even just in the shot shell facility.
Grant Jeremiah: there's, I can't have a number on it.
Ben Frank: Several hundred. Oh, it's, it's hundreds if not over a thousand. When you're talking individual SKUs, when you're talking different shot sizes, a lot of things that we do are, are similar, right? So, if you're making expert, 15, 50 ounce and an eighth, three inch stuff, okay? So, we have four shot, we got six shot, we got BBs, we got twos, threes, sometimes one. So, you know, there's, it's very similar, but Each one of those things requires us to change the equipment, put new packaging on there, carry different inventories of different things. So, it's a lot to manage, but the way we pick those things is by what our consumers want. There's a lot of people who, when it comes to waterfowl hunting, not everyone's scenario is the same. We also know that. I may hunt a certain way and Grant may hunt a completely different way. talk about Illinois here, it gets pretty tough from time to time. You got to find where the birds are at and it might be a little rough. You might want to use dry lock because I might be standing in three foot of water constantly. Whereas somebody else, and I might have to be shooting birds that are maybe past shooting some of them a little bit more often where they're not right in your face versus somebody else who has them coming right in. We want to be able to make sure that if they want threes because that's their magic sauce, we got it for them. So that is another thing for us, the fact that we can build so many things so quickly, we can provide pretty much the entire gamut of products, whether that's opening price point expert, that's going to be your best value for what you can do there with that product, all the way up to a last call type product, which is 100% TSS 18 grams tungsten, which is going to be the best of the best.
Nathan Robinson: That's actually a good topic to bring up because sometimes it can be confusing how many products we have. And in the waterfowl space, that's certainly the case, but it's because we're trying to hit those different price points and different applications. And so we want to be all things to our customers. And so that means there's a lot of skews. from a marketing perspective, that's fun trying to figure out how to promote like six different brands, but we certainly don't want to shortchange our customer and dictate what they can use. We want to give them a lot of options.
Mike Brasher: The thing that impressed me as I came out of the tour was the focus on quality control, the testing, all the different shops that we went into, all the different electronic, all the technology that's now included in this, kicking out shells that don't meet up to some standards. And then once you do get the shells that do meet the standards, then they go through rigorous testing and through some, I don't know what we call them, the shooting facilities back there. You talked about some of, you actually have Nilo farms where you actually test it out of a gun, shooting the birds as well. But I just, I can't imagine the I never… I think I took a lot of that for granted in terms of the amount of testing and quality control that goes on with all these different products. I mean, how much pride… How important is that in the grand scheme? It's one thing to make a shell. It's another to demand an incredible amount of consistency and put in place all the different things to ensure you get that.
Grant Jeremiah: Yeah, I mean, like you said, there's a lot of pride there. And it is. Every single component, we look at each one individually and how we can maximize that for that specific application. I mean, we looked at different machines for different applications, whether it's for target loads or for waterfowl like we're talking about now. I mean, the components and everything are all completely different. Some of the stuff might be similar, but generally the way we manufacture it, and it starts at a ground level. I mean, it starts with all the employees out there working on the machines all the way up to our president. I mean, we all come together and sit at the same table figuring out how we can make the best shell.
Ben Frank: And I'll say, I think people take for granted a little bit, or maybe don't realize, I wouldn't say take it for granted, but the level of detailed testing that we do. So for instance, we test our components on waterfowl through very rigorous situations, meaning we'll test it all the way down to zero degrees. Most people probably aren't hunting at zero degrees, but there is that possibility. all the way up to 125 degrees. And the reason we do that is plastics do not like those kinds of temperatures. You have to do special things and you have to design that plastic component just right to be able to work in all those scenarios. Because if you don't, your consistency is going to be bad. If anything, you could actually start causing issues with squibs, low reports, misfires, things like that. And we also test all of our waterfowl products through water testing. So, we're not saying those things are waterproof, because there's so many different scenarios that can happen. But when it comes to water resistance, there's really no products out there like Winchester, and we test them. We test everybody's stuff. And time after time, there's no one that really comes even close to the consistency of ours when it gets wet. And yeah, okay, again, some people might not have to worry about that. You can shoot expert all day long, or you can shoot some of these other ones out of a dry blind. But if you're gonna be sitting there getting wet, maybe your coat's getting dunked in the water, and then you're not getting it dried out afterwards. I mean, once water gets in your shell, it's pretty much in there. It's gonna be tough to get out. And our shells are going to work in those situations consistently time after time. If you're seeing issues with other stuff and it, you know, you're getting a misfire or you're getting weird sounds, or that's probably the norm for those folks because that they don't have those kinds of componentry. They don't have that kind of backend testing that typically is just par for the course for Winchester.
Mike Brasher: And let me tell you, you don't want to misfire when you have a green-headed mallard hanging over the decoys at 20 yards, right? No.
Ben Frank: No, you do not. Nope. And you don't want bad things like a wad getting stuck in your barrel either. Those kinds of things are bad news. And I would say that waterfowl hunting is probably one of the most harsh conditions that you're going to typically find with really any ammunition. Yeah, of course there's plenty of folks who never are dealing with those kinds of conditions, but I've been in some places where it's really nice and you think this is going to be easy and it's cold and it's raining and you're still getting all wet and you've got water pouring down your barrel. If you want to have a successful waterfowl season, you're going to be dealing with those kinds of conditions and we know that. And we've known that going back decades to the John Olin days and we've only continued to improve those things throughout time.
Mike Brasher: You've mentioned it a couple of times and I want, this is kind of for my personal education and I know our listeners will appreciate this too, you mentioned dry lock. as a sort of, is it a waterproofing technology? I'm looking at the back of the bismuth box here that we have and it says water resistant lacquered primer and double seal wad to keep out the water. Is that different from the dry lock technology? It's basically, that's the dry lock technology.
Grant Jeremiah: Yeah, that is the dry lock technology. We utilize that double seal. So, we're allowing the water to actually get in with a shot because there's really no way to keep it out there. And you can put seals on the
Ben Frank: I actually grabbed a couple. The people listening aren't going to be able to see this. So, this is your double seal. This is one that's got like a hinge. I saw you all grabbing for your pockets.
Mike Brasher: I'm like, what's going on here?
Ben Frank: Well, seeing is believing, right? So, but when you look at these wads, both of them, these are our powder cups, let's call it. So, these are the dry lock powder cups. And this one, we're able to use this, if you can't, you you're not watching and you're listening, there's some hinges there. And that's really kind of helps cushion the firing as well as if you have a lighter payload, you can fit a hinged member in there. And then this one here that doesn't have a hinge, this is the original Drylock wad right here. And what really makes Drylock special is that it's really an interference fit. So, you're basically creating this interference between the tube wall inside of the tube and this wad. And with plastics, plastics move, right? So, but you gotta be careful. You put too much interference in there. You get, your pressures rise. It's hard to get velocities where you want them to be. So, it's, it's a balancing act. A lot of different, again, iterative testing that went into these Drylock powder cups to be able to make these work and even to get them in the shell and stay in there. Because when you have that- It's an airtight fit.
Grant Jeremiah: Yeah, I mean- They want to, they want to pop out of the shell because you're creating that hydraulic pressure underneath with the, with as you try to squeeze them in.
Mike Brasher: What are the test metrics that you're looking at on something like that? You said this iterative testing and all that. I mean, how many different things do you look at in that test?
Ben Frank: Well, you look at pressure and velocity. So, CME, Nathan mentioned them before, but they dictate certain pressure levels that are safe out of firearms. And we stay within those pressure guidelines throughout the different temperatures. So, you don't want to be loading something at 70 degrees and you think you're okay, and then you go and shoot it at 20 degrees and all of a sudden the pressures are out of sight. So we test all of those different pressure ranges. We test patterns with it, which typically those won't affect your patterns too much, but we also recover the wads. So like at those different temperatures, again, plastics can have things go on with them that we want to make sure it doesn't happen. Like we don't want this thing cracking in half. And if it gets brittle or we make it from the wrong material or it's not the right thickness or any of that kind of stuff, that muzzle, that flash from your primer could cause problems and break this thing. So, there's a lot of testing that was done to make sure that doesn't happen. So, consistently at all different temperatures, that thing is surviving. It's providing consistency. So, we test variation, it's called. So, like our extreme variation. So, high to low. How far are our high pressures to our low pressures? the high velocities to the low velocities because we don't have a lot of variation. That's good because we're staying consistent. That's our goal is to be consistent and consistently meeting what we're saying that the velocities are and our patterns are going to look like.
Grant Jeremiah: We do also do a multitude of water tests as well. We'll actually take a bucket of ice water, throw the shells in there, let them sit in there for a certain amount of time, take them out and shoot them. And then we also do that in checking velocity, pressure, all of those same things after they've been wet.
Ben Frank: I think my favorite test is the one, so like when you put them in a bucket, most of the time water will get down in there, but when you inject them with water to make sure that they're getting water in them, that's the harder test. And again, that's my favorite because whenever we test it, our stuff's always head over heels better than anyone else's because usually next to nobody can survive that water injection test. And the water injection test is really meant for, hey, this stuff got in there. We're going to force this to be the worst case scenario, which someone will find out there. And how do we make sure that our mousetrap continues to perform? And we test it. We make sure that that's the case. So, that's my favorite.
Mike Brasher: Nathanael So, I'm pointing at the bismuth and last call. And any of the other waterfowl loads have anything to help prevent water from from getting inside and sort of at the crimp, the top of the shot shell. I don't know if that's, yeah.
Grant Jeremiah: Yeah, we do seal the crimp with glue. However, that's more to keep the internal components in, especially if our buffered loads. We do find that the sealant there doesn't work as good as what you'd like, just because of the way the crimp's formed itself. You get little holes. It does work to an extent, but we found the best way is just to keep the powder dry with the Drylock WOD system. That is the most consistent.
Ben Frank: Yeah, and what you'll find, whether it's our stuff or everybody else's, you're going to get water. If it's in enough water and it's down deep enough in your pockets or whatever, it's going to get through that crimp. It's really stopping it from getting to your powder. I mean, you don't want that water to get to the powder or the primer, and that's really where ours shines. Another piece of the puzzle is, especially on premium steel, is plating that shot. So, if you don't have plated shot, which most Most manufacturers, including ourselves, have plated shot. It's going to pattern the best after it gets wet because it resists any kind of rusting. I mean, steel can rust. You don't have to worry about it with tungsten and you don't have to worry about it with bismuth, but with steel, you do. So, the premium steels, if you're using a premium steel, it's typically plated.
Mike Brasher: Both the last call and bismuth talk about how it's buffered shot, right? Buffered tungsten and buffered bismuth. Talk about that. What does that mean? I think I heard a little bit of that on the tour.
Grant Jeremiah: Yeah, so our bismuth, we do buffer that. And that buffer actually just goes and fills in the interstitial space in between the pellets. So bismuth itself is inherently brittle and it wants to fracture. So we alloy our bismuth with tin. That helps makes it a little more ductile metal And then once you add that buffer in, that's really what keeps it round and what keeps it from fracturing. So, it comes out of the barrel completely round. It makes for great patterns, makes excellent shot shell, far above what we see out there that's unbuffered. And so, that fills in all those little spaces, like you said. And then with our tungsten, the buffering in there really is more to help with one for load fit, but also it helps it flow through choke tubes a little bit better because that is such a harder shot. That one won't deform where bismuth can flow a little easier. Tungsten itself kind of needs to glide through those choke tubes.
Mike Brasher: What else do we want to talk about with regard to any of the new products here, Bismuth or Last Call or anything?
Nathan Robinson: I would just point out a connection here. So, Ben was talking about the plastics that we use in our hulls and in our shot cups and all these components. Our scale allows us to do more testing and to build a better mousetrap like he described. And it's the same thing with our bismuth. If you see another bismuth on the market, they're not the same. Everybody has different levels of metals alloyed together for different benefits. And so we're able to do more engineering on the back end to optimize that alloy so it'll do what we want it to or add the correct buffer. Just things that the scale of Winchester is able to flex on in the industry because we do have all those buildings full of engineers with nothing better to do than to think of how to improve it and make it better and keep testing it and really doing the best that we can for the market.
Ben Frank: I'll mention a couple things on these two because best of the best stuff. One of the key features around bismuth or last call is really the use of those small gauges. So, you think about, you mentioned it. Yeah, I got a 28H now, you know. And I mean, they, they truly make those small gauges very viable options and they're a lot of fun because they, they're limiting the recoil. I mean, one of the things that, you know, whether you're old, young or indifferent, it's, it's not a whole lot of fun to get beat up all day. If, especially if you're missing, you know, and a lot of times you're going to end up shooting a lot better. and having better shots on target. If you're not dealing with recoil, maybe you're willing to spend a little bit more to be able to get that added benefit of that reduced recoil. And when you look at the pattern density and the number of pellets that you get with something like a last call, because the density is so high and you're using these small, like number nine pellets, you end up having a 410 load that has almost as much as a 12-gauge steel shot load.
Grant Jeremiah: It's very similar to a 12-gauge 3-inch number 2 in terms of pellet count. And that number 9 TSS will penetrate more than a number 2.
Ben Frank: So, you can use, effectively, the penetration, the on-target, like, you know, knock them down type energy that you're looking for. You have that and more out of a 410 No. 9 than you would out of your 12-gauge ounce and a quarter No. 2s. Bismuth, not quite as dense, but still kind of similar story, but you're going to be able to get bismuth at a lower cost than, say, TSS. Is that balancing act between cost and performance? But again, those small gauges become a lot more viable when you're using something beyond steel. Do we offer steel shot in those small gauges? Absolutely, we do. But you start talking, it's not a lot of pellets, so you really got to get them in tight. Whereas these, you can actually use these small gauges and get similar performance that you have out of your 12-gauge steel shot loads, which is pretty awesome.
Mike Brasher: You talked about patterning and some of the properties of last call and bismuth. Is that part of your testing? And at what ranges do you test and how does all that work? I'm really glad you brought that up. Because there's a lot of iterations for patterning. Yeah. And we talk about that for people, for individual hunters, but we're talking about it for Winchester, we have however many skews that we talked about a moment ago.
Nathan Robinson: So before they jump into what we do on the science in the back end here, turkey hunters have had that figured out for years. And I think duck hunters are just now starting to realize that it's important to pattern and there's not like a consistent rule across all ammo. And so if you guys want to pick it up from there on what we've seen in our testing.
Ben Frank: I'm just going to add that. Okay. So like, as you said, TSS has been around for a while now. And there's even been some waterfowl loads out there with TSS. But what we wanted to do is just like with anything we ever do in Winchester, we're not just going to take that particular load spec or shot size and say, you know what, that'll work. Most of us in here, when it came to TSS, hadn't shot much of it at waterfowl. And so we really needed to look at what is the most optimum shot size for this situation? Is number nine shot going to work on Mallards? We have Grant and his team doing gel testing that we would do typically on any other stuff that we use. We'll take it out to Nilo and we start using it on those birds just to kind of see, okay, yeah, everyone's using number nines. Is that what you need to be using? Or should we be using sevens or even eights? And, and those are the kinds of things that before we ever even tell anybody we're even going to do it, we're doing that backend testing to ensure that we like the patterns. We like the pellet count. We like how it performs through different choke tubes. And, and you know, all of those things happen versus us just saying, you know what, everybody likes number nines. Let's put number nines in there. So it's, it's a lot of fun. And I'm sure Grant thinks it's a lot of fun because him and his team are the ones getting the hand loaded every day, but it's,
Grant Jeremiah: That's what we do. It's definitely a lot of fun. Yeah, I mean, we spend a lot of time patterning. I mean, we shoot a ton of patterns.
Mike Brasher: I mean, generally when we… Do you shoot it off the shoulder or do you use some of the testing range that we saw in the facility?
Grant Jeremiah: We do use the testing range in the facility for most of the stuff.
Mike Brasher: To save your shoulder and kind of cut down on medical bills and things like that, right? Yeah.
Grant Jeremiah: Well, and not only that, but you also cut out external factors like wind. I mean, believe it or not, wind actually matters quite a bit. I mean, even when you look at tungsten dropping at 60 yards, you're dropping an average of about six inches in number nine shot. So, that's something that you got to take into account as well. But yeah, in our facility, we're able to shoot patterns at, you know, 40 or 60 yards and even different ranges if we're trying different things. You know, we check various choke tubes, various guns. I mean, a ton of patterns. And it's not like we just shoot one pattern with each gun. You know, we'll do a multitude and then get an average off of that.
Mike Brasher: The thing that I was probably most surprised at on the testing was when I asked, how frequently do you do the test firing, I guess, to check the quality and the performance? And was it four times a shift? Four times a shift every two hours. Which is incredible. And you do that for each of the products coming off the line or does it at that time? Because as we were going through, I don't know how many products were being produced at that particular time. I mean, those are the ones that are coming off. And so, you do that testing for each of those?
Grant Jeremiah: Yes. It does depend on some of our products. Some of our higher-end products or some of our products that maybe we're running a little bit lower volumes, we're going to grab more frequently off the line to do more checks. Some of the stuff that we, I mean, two hours, that's our average. I mean, not an average. That's what we do the minimum. So, some of those products, like I said, like this TSS Last Call or our Bismuth, that stuff we're going to check even more often to make sure it's a premium product. We're going to make sure we stand behind it.
Mike Brasher: So sitting behind us over here is Jake Wallace. Not mic'd up. Jake's not mic'd up. Remind me of Jake's title. I forget. I know Jake as the Winchester sharpshooter, the professional shooter that was with us last year down in Louisiana. I would encourage folks to go back to episode 539. That's where we talked about our are duck hunting and snipe shooting exploits. And so that was a fun trip, fun time with folks from Winchester there. And my question is, what role does Jake play in any of this kind of quality control and testing when it comes to actually the live firing and testing on birds?
Ben Frank: We let him go out to Nilo and shoot with us. We let him go out there and show us up from time to time. But no, Jake has had a very prolific career. If you look him up in the Olympic shooting world, USA shooting international and international trap is one of those things that I've, I've never done. But when he tells me about it, it's like, no, the difficulty level is way up here compared to your standard trap shooting. And you know, he, he shoots double A's probably partly because he works here, but probably because it's the best of the best stuff. And you know, it's, it, it truly in those situations, every single shot matters. I mean, I'm speaking for him here, but I I've heard him talk about it and you know, that's, you got to have the best of the best in those situations. And we strive to do that in our AA line. And again, it carries over throughout all of our shot shells. I'm sure he's a pretty good shooter across the board. Anyone who does a lot of practicing, it's like Nathan was talking about patterning your gun. If you want to become a better waterfowler, go out and practice, go shoot sporting clays, go shoot trap, really any of those kinds of things kind of gets you familiar with your with your firearm. Jake would attest to this because practice makes perfect. And especially in the waterfowl scenario, you just never know where they're coming from or how far your shots are going to be that day. And the more you practice, the better you're going to be. And the more you try out the ammo that you have, you get familiar with your entire setup. And I know again, Jake and folks like Jake, that's a big deal for them is continuing to test their equipment to make sure that it works every time, and they know what's going to happen. They know where it's going to drop. They know if it's a windy day, what to do, so.
Nathan Robinson: I think that's the golden nugget of this whole conversation. It's fun for us to brag about a company and product we care about, but for the listeners, they should take their loads out and practice with it, because some ammo will work best with a wad stripper type choke. Some will work best with an IC factory choke, and you don't know until you actually get out and shoot paper with the specific ammo that you're going to use, and so we encourage people to do that.
Grant Jeremiah: Yeah.
Nathan Robinson: And you probably got some data you can share on that too, right?
Grant Jeremiah: Yeah. And your specific experience is going to vary across the country. You know, if you're shooting in the timber, it's going to be completely different than if you're on public land shooting passing birds. So, I mean, just try to tailor what the ammunition, your gun, your choke tube, all that to your experience. So, give you the best possibility of, you know, success in the field.
Mike Brasher: What else, guys? We've covered a lot. We started and you asked about how long you think we'd be able to talk on this. We could keep going. We're already at about 50 minutes. I think this is a pretty good place to wrap up unless you guys have anything else to offer here.
Ben Frank: No, I appreciate you letting us kind of walk through it. This stuff for us is near and dear to our hearts, not just our job. It's something that we really enjoy. We love talking about it. I mean, it's like you said, going back to the end of the day, whenever you're like, did you think you were going to work here kind of thing? It's like, no, but I'm glad I do because I'm getting to talk on a podcast about, you know, waterfowl hunting and how do we this group of people here that, that work here at Winchester get to make that experience cool for people. And that, when you, when you walk through a store, when I walk through, you know, a retailer and I look at shelves and I see our products and I say, you know, we helped put, put that picture on that box, but we also helped put that wad and that shot and that primer and all the people that went into that. It's just a cool feeling to know that you're a part of that.
Mike Brasher: So, does that mean that when you go duck hunting, waterfowl hunting, that it's actually work? Because you're actually trying out the product?
Ben Frank: That's what I tell my wife. You have to do this.
Mike Brasher: Gotta go test out these products. Guys, I really appreciate the opportunity to be here today, to visit in person, to get the behind-the-scenes tour. It was fascinating. I learned a lot. As I said, having done a bit of reloading when I was younger, I was able to understand a little bit more about the components. And I think it gave me a greater appreciation for actually what I was doing back then and the reason that I chose AA as the shell to reload and chose Winchester wads and all of those other things. And so to kind of make that connection was pretty cool, again. Thank you guys for everything you do. Thank you to Winchester for being the official ammunition of Ducks Unlimited. I know we'll have other opportunities to get together, but again, a truly iconic brand, two iconic brands, Ducks Unlimited and Winchester.
Nathan Robinson: And we'd be remiss not to thank you. So thanks for making the trip up to see us. Thanks for all the science and study you're doing. Our ammo doesn't do any good if there's not ducks flying. So we appreciate the work of DU and you specifically.
Mike Brasher: That's right. Well, thank you guys. So for Ben Frank, Nathan Robinson, Grant Jeremiah, I'm Dr. Mike Brasher thanking you all for joining us here. We will also extend a thank you to our producer, Chris Isaac, who does a great job with these episodes. And then to you, the listener, we thank you for your time. We thank you for being waterfowl hunters. We thank you for caring about this resource. We especially thank you if you are a purchaser of Winchester products. If not, go give them a try. They have some fantastic new products coming out. I encourage you to give them give them a try. So thanks, everybody. We'll catch you on the next episode.
Creators and Guests
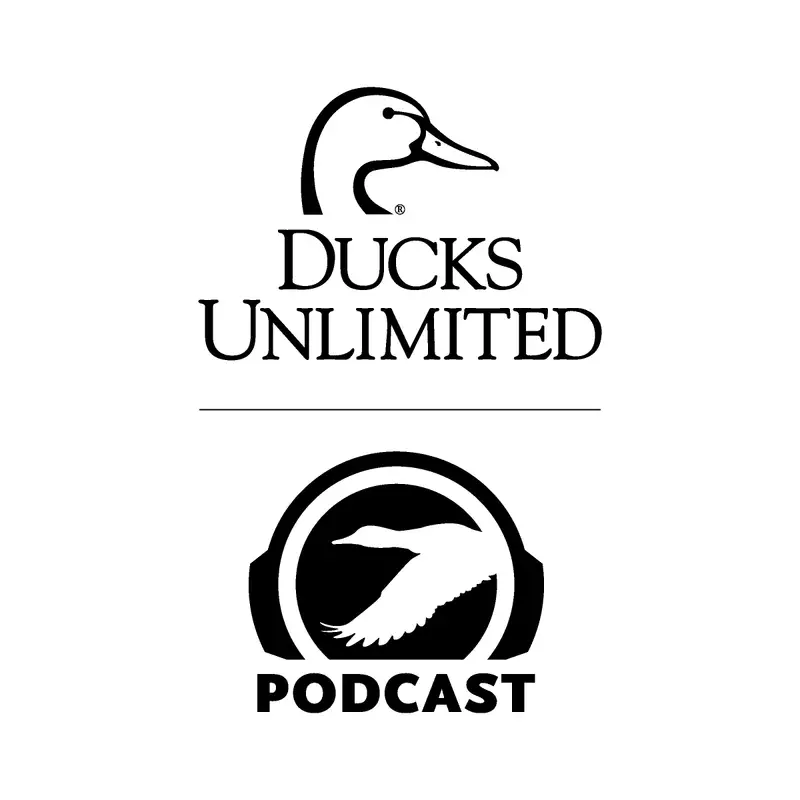